As food processors all across Europe face unprecedented cost pressures, economization has become essential to the survival of many businesses. Investing in a JBT Frigoscandia GYRoCOMPACT® self-stacking spiral freezer is one of the quickest ways to cut your energy, water and manpower costs whilst becoming more efficient in the process.
In fact, customer data indicates that a self-stacking spiral freezer can cut energy costs by up to 60% compared to a traditional drum freezer.
So far for Europe’s food companies, 2022 has delivered the perfect storm. Soaring inflation and rising utilities costs have put much pressure on many processors in an industry where margins are often slim and retailers are constantly demanding lower prices.
In such an environment, the ability to cut costs whenever possible is crucial, and one of the simplest ways is to replace inefficient freezer units with more cost-effective alternatives.
JBT Frigoscandia’s GYRoCOMPACT self-stacking spiral freezer offers a number of significant advantages. As JBT’s Sales Manager, Jan Grundmann, explains, the GYRoCOMPACT delivers immediate energy savings upon installation thanks to its effective, efficient design.
“In a recent meeting with a customer who uses both systems, the customer’s data revealed that their GYRoCOMPACT freezers consume up to 60% less electricity compared to their current drum freezers at a comparable product-throughput,” he says. “This particular example equates to a potential annual savings of more than €300,000. This may sound too good to be true, but the customer’s ledgers from their daily operations clearly demonstrated that a freezer replacement was justified due to the quick return on investment.”
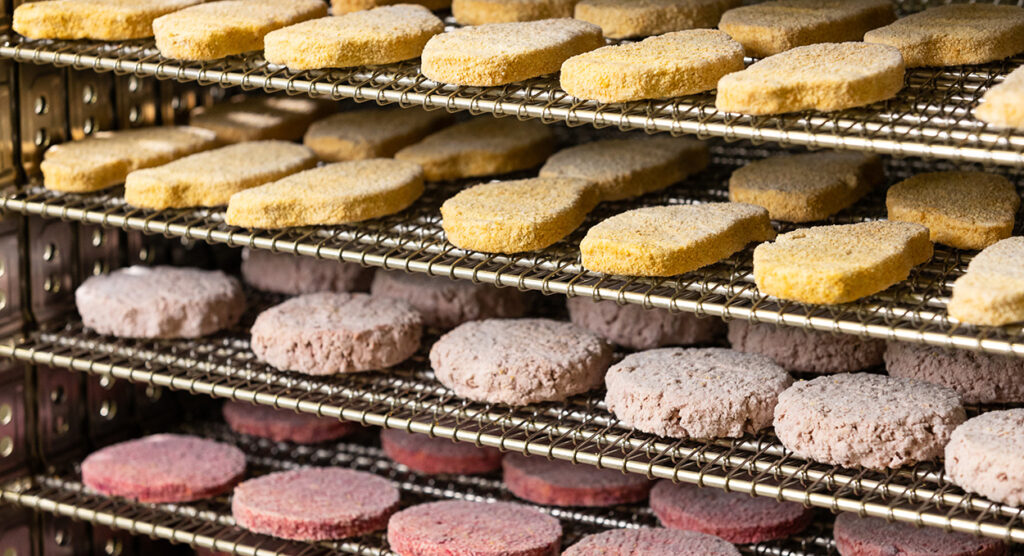
Widespread savings
JBT’s self-stacking freezers don’t just make a difference in energy savings, they also have a positive impact on other utilities, such as water consumption, and cut down on, among other things, manpower and time.
Due to its minimalist design, the GYRoCOMPACT amounts to 12 tonnes less installed material than a traditional freezer system. This means there is significantly less area to clean.
“On traditional freezers, many of our customers complain that product residues remain on the belt-support frames, which requires a lot of additional cleaning,” Grundmann continues. “As we simply have less material and fewer corners and surfaces, we ensure a 100% cleanable product-zone with the GYRoCOMPACT. This means far less time and far fewer people to maintain optimal hygiene.”
In fact, a GYRoCOMPACT typically only consumes about 20% of the manual cleaning resources needed for a traditional system, leading to considerable savings in manpower, time and water consumption. “There are customers who report up to double the cleaning time, three times the water consumption and three to five times the number of cleaning staff needed for their drum-freezers compared to their GYRoCOMPACTs,” says Grundmann.
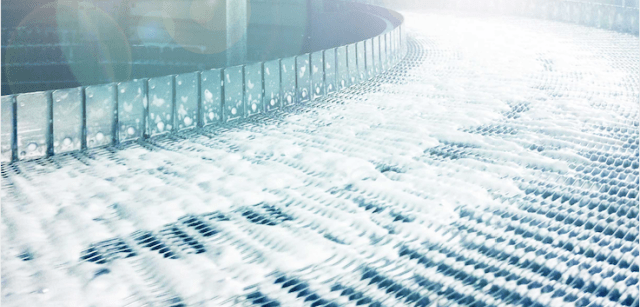
Helping to fight inflation
In recent months, a major European customer developed a keen appreciation for the advantages of a self-stacking freezer compared to a traditional drum freezer. The customer, as Grundmann explains, had previously only owned JBT freezers but made a decision to invest in a competitive drum unit several years ago.
However, product-related and technical issues soon emerged, forcing the customer to revisit this decision.
The final “go-ahead” to replace the freezer with another GYRoCOMPACT unit was made based on the potentially significant cost savings of the freezer. This ended up becoming the largest cost reduction in the entire processing line, making it an integral part of the customer’s fight against inflation.
“In many cases, customers don’t replace JBT freezers even after 30 years. This gives you an idea of the situation since the customer felt compelled to replace a drum freezer after only five years,” Grundmann adds.
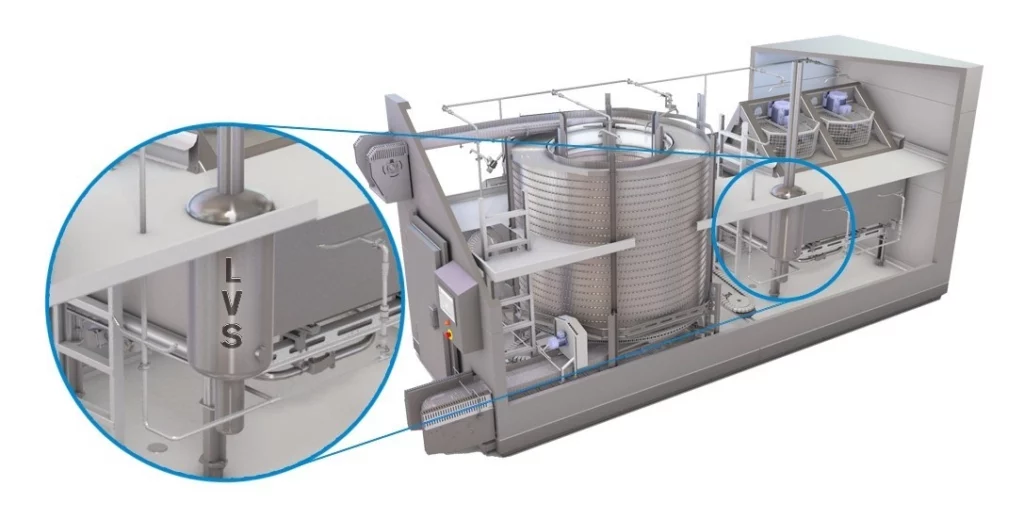
LVS delivers additional savings
The GYRoCOMPACT can be supplemented with the LVS (Low-Volume System). This add-on unit, which has been developed to improve freezer efficiency, is up to 20% more efficient than traditional pumped refrigerant systems. The LVS’s patented dry-suction system delivers more compressor capacity and enhanced evaporation, all of which add up to improved freezer performance.
In a traditional pumped refrigerant system, pressure drops lead to temperature losses of between 3 and 5 °C. With an LVS, customers only lose 0.5 °C, even over longer pipe distances.
On top of the savings already generated by the GYRoCOMPACT, the LVS can deliver an additional 15% reduction in refrigeration cost compared to a traditional system.
LEARN MORE about the JBT GYRoCOMPACT and LVS systems
Are you interested in an all-electric food processing line for your plant-based product?
Book a meeting with one of our food processing experts to learn more!
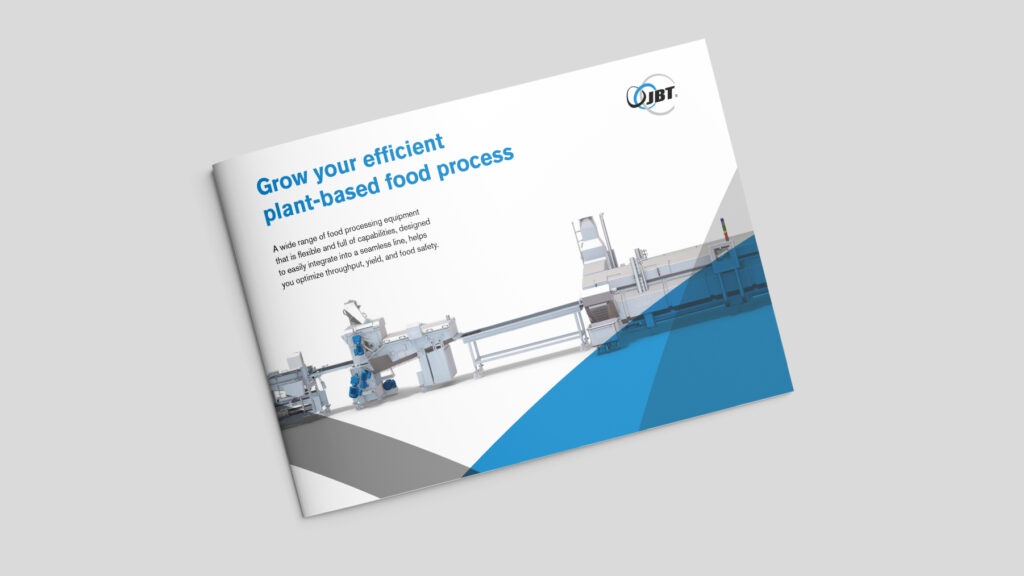